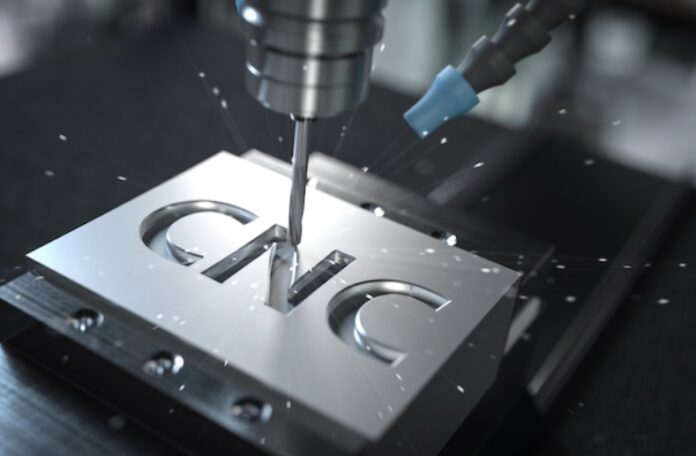
Industry 4.0 has been underway for a while — a new industrial sector with more significant potential and efficiency while leveraging automation and robots. The fourth industrial revolution is far from over, as new technologies enter the market daily, and the debut tools that began the transition continue to flourish. CNC machining is one of those investments most manufacturers deem essential.
What Is CNC Machining?
Computer numerical control (CNC) machining relies on programming. Experts input orders into programs that tell manufacturing machines what to do with each processed order. CNC is as simple as that. It embraces automation and efficiency as a remote operation takes the manufacturing sector by storm because it promises to improve quality of life and profitability.
The CNC machine market is expected to increase in the U.S. by at least 5% over the next several years, equating to $126 billion in 2030. Several major types of CNC machining companies could leverage include:
- Turning: Lathes that can remove materials from the workspace as it operates to execute everything from embossing to finishing.
- Electric discharge machine (EDM): Uses electricity to manipulate materials.
- Grinding: Primarily for automotive parts, grinding uses a rotating wheel when shaving out its projects.
- Plasma: These use torches to work through even the most rigid materials, like stainless steel.
- Water jet: Uses powerful water streams to manipulate materials.
- Pick-and-place: Sometimes, in the form of robotic arms, these machines automatically do as the name suggests, generally manipulating smaller materials like phone parts.
CNC programming executes the process if a car manufacturer needs a lathe to cut a metal part via a template. If a programmer wants a tool on a production line to move objects, it only needs a prompt. These examples highlight only a few CNC machining capabilities, so the manufacturing sector gravitates much to these machines. It embodies the feeling of using robots without robotic assistance.
What Are the Pros of CNC Machining?
Countless manufacturing enterprises are banking on the promise that CNC machining will improve their operations. Is there proof of the hype, and can it outweigh potential drawbacks to the power?
Increased Computational Power
The predecessor to CNC machining was numerical control machining, and its input was not clean computerized codes — they were punch cards. These mediums limited the power of machinery. But now, programs can store and execute more extensive, complex commands without technical exertion.
The executables, changes, and previous controls sit in a database, stored for continued usage with easy access. These controls are malleable and adaptable, whereas punch cards were one-and-done processes. With CNC, every command has a chance to grow and get better from its initial form.
Eliminates Trial and Error
Traditional manufacturing blueprints must undergo several CAD iterations before a final product. That equates to wasted time, money, labor, and materials. CNC machines run through those simulations before starting a job. There isn’t a need to wait for prototypes to fall onto the belt if the prompt shows signs of process improvements for programmers.
Reduced Waste
Eliminating trial and error eliminates waste in the pre-production process, but what about during? CNC programs automate material use by following predetermined paths and functions, making the most available. Having pre-assigned programs also helps monitor energy usage consistently.
Plus, connected technologies that demonstrate waste analytics could help corporate sustainability initiatives more by providing actionable results that can improve CNC inputs over time. It’s not a conclusive waste-reduction strategy but a great supplement.
Removing Human Error and Safety Concerns
Manufacturing jobs aren’t without their dangers. The less worker’s comp a company has to pay out, the happier — and safer — everyone is. Using CNC means remote operations, putting fewer workers in harm’s way. The minimal human involvement does not mean CNC machines will phase out human workforces — as they will still perform inspections and maintenance — but will influence production meaningfully.
Most industries have countless losses from human error, and manufacturing isn’t an exception. Long swing shifts lead to tired staff with quickly depleting endurance. Mistakes are expected with that kind of morale, and CNC could reduce those feelings in technicians, helping their health and wellness as a byproduct.
What Are the Cons of CNC Machining?
There is no such thing as flawless technology. CNC machining will eventually pave the way for another automation tool humans can’t conceive yet. So what will that aspirational technology have to improve upon with current renditions of CNC machining technology?
Prompts Can Ignore Machine Status
CNC programming happens no matter what. If the code is there to initiate a prompt and the machine is on to receive it, it will happen. The reliability is ideal, but not if the device isn’t in working order. Severe consequences might happen to the process order or the machine itself if plant technicians ignore routine maintenance and the CNC commands, telling it to persist despite that fact.
Programmers and engineers could instill novel preventative measures that force prompts to evaluate machine health before beginning, but that isn’t a feature naturally embedded into CNC programs.
High Upfront Investment
The promise of returns sounds ideal, but those are gradual financial gains over the years. Those profits are difficult to quantify for instant gratification, and the hefty price tag of CNC machining at the start is reason enough to look the other way.
Companies can hire third-party CNC machinists, who can allocate their hourly rates for machine use. Or, manufacturers can install on-site machines, earning the best return possible if they’re well-kept. Lowering costs is possible through clever design, like limiting thread lengths and tight tolerances.
Lack of Qualified Technicians
The most considerable oversight of Industry 4.0 is the need for more qualified workers. Tenured skilled workers who have been with manufacturers for decades haven’t had formal education and rare training opportunities throughout their careers. Companies must institute programs to get techs to meet new qualifications out of their control and comfort zones.
It’s an added expense on top of the technology, and a lack of experience could lead to production hiccups. However, that’s a certainty when adopting new technology, no matter what sector.
Is It a Beneficial Investment for Businesses?
As demonstrated, the benefits surpass any negatives by a mile. The pros don’t stop there because there are many other reasons CNC machining and milling easily convince businesses to invest.
CNC machinery could bolster those efforts by accenting that mentality if companies aren’t already going through digital transformation and implementing digital operations. It’s essential for manufacturers and material workers to embrace the value of digital assets and automation to stay relevant internally and for business partners.
Once antiquated manufacturing companies mentally transition to Industry 4.0 mindsets, they can start scaling their operations and machinery accordingly. CNC helps with scalability because of its versatility. Companies use as few or as many CNC products as they learn and adapt to them. Internal policies and operational procedures will have to change over time, and technicians will have to know them too. The transition can be as slow and seamless or aggressive and drastic as companies want — but CNC machining gives them that freedom.
The faster assembly will give workers more room for high-value tasks around production lines. It will give them time to scale their skills to meet modern needs. At the same time, CNC machining creates products with unparalleled precision and accuracy, even alongside other high-potential technologies like 3D printing.
These time openings allow manufacturing enterprises to experiment. They could expand what products they make if their CNC machines provide capabilities they previously didn’t have, or at least, at the scale that had a decent cost-benefit analysis. CNC machines could use unused materials on some production lines, ranging from wood to brass, innovating products or adding new ones to lineups that earn companies more money and diverse customers.
They could have all this without sacrificing quality, as the CNC machines help manage quality control with human intervention. Consistency equals fewer defects, which signals happier customers.
Making a move to CNC Machinery
If the excellent press around these technologies isn’t clear, every manufacturer should transition to CNC operations. The tech has too many comprehensive benefits, and the drawbacks are manageable with additional effort. It’s difficult to say if companies that refuse to adopt CNC will fall behind, but it’s likely. The accuracy, efficiency, and savings these technologies offer are worth making the necessary changes.