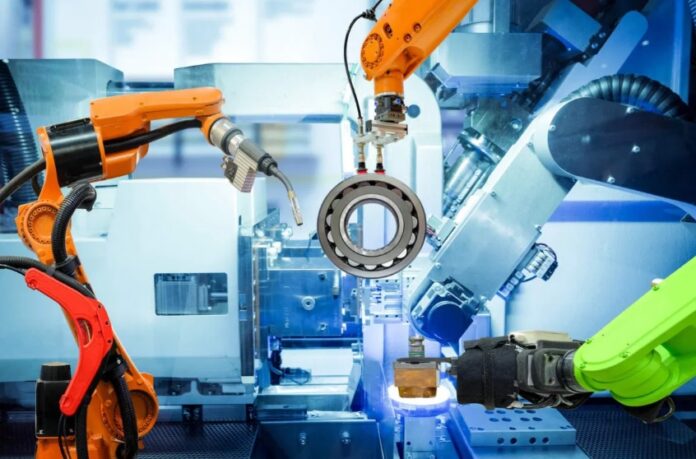
Product recovery systems are revolutionizing industrial applications by minimizing waste and maximizing efficiency. These innovative solutions capture and reclaim valuable materials that would otherwise be lost during production processes. By implementing efficient product recovery solutions, companies can significantly reduce costs associated with raw materials, waste disposal, and cleaning operations.
Product recovery techniques encompass a range of methods, from pigging systems that clean pipelines to clean-in-place (CIP) systems that sanitize equipment without disassembly. These systems are particularly valuable in industries handling paints, coatings, lubricants, and adhesives. They excel at recovering products from challenging environments, including those with aggressive temperatures and chemicals.
The benefits of product recovery extend beyond immediate cost savings. By reducing waste and improving resource utilization, these systems contribute to a company’s sustainability efforts. They help lower environmental impact by reducing emissions and minimizing the carbon footprint associated with production processes.
Key Takeaways
- Product recovery systems reclaim valuable materials, reducing waste and operational costs
- These systems improve efficiency in various industrial applications, from paints to lubricants
- Implementing product recovery solutions enhances sustainability and resource utilization
Foundations of Product Recovery Systems
Product recovery systems form the backbone of sustainable industrial practices, minimizing waste and maximizing resource utilization. These systems incorporate innovative technologies and processes to reclaim value from used products and materials.
Understanding Product Recovery
Product recovery involves collecting and processing used items to extract usable components or materials. It aims to reduce product waste and emissions while improving profitability. Recovery methods include remanufacturing, refurbishing, and recycling.
Remanufacturing restores used products to like-new condition. Refurbishing involves minor repairs and upgrades. Recycling breaks down products into raw materials for new production.
Effective recovery systems require careful product design, efficient collection networks, and advanced sorting technologies. Companies implementing these systems often see improved return on investment (ROI) through reduced material costs and new revenue streams.
Technological Innovation in Recovery Systems
Technological advancements have revolutionized product recovery processes. Fully automated, PLC-controlled systems enhance efficiency and yield in material reclamation.
Pigging systems, for instance, recover residual product from pipelines in food and beverage industries. These systems use specialized devices to push out leftover materials, reducing waste and cleaning costs.
Advanced sorting technologies use sensors and artificial intelligence to identify and separate different materials quickly and accurately. This improves the quality and value of recovered materials.
Innovations like VIPRSĀ® (Versatile Industrial Product Recovery System) offer customizable solutions for various industries, maximizing recovery rates and minimizing downtime.
Environmental and Economic Benefits
Product recovery systems significantly reduce environmental impact by decreasing landfill waste and conserving natural resources. They help companies lower their carbon footprint and improve energy efficiency.
Economically, these systems offer substantial benefits. They reduce raw material costs, create new revenue streams from recovered materials, and can lead to financial rebates or tax incentives in some regions.
By extending product lifecycles, recovery systems help companies comply with environmental regulations and meet consumer demands for sustainable practices. This can enhance brand reputation and market competitiveness.
Implementing recovery systems often requires initial investment but typically results in long-term cost savings and improved operational efficiency. Many companies report positive ROI within a few years of implementation.
Implementation Strategies and Case Studies
Product recovery systems offer significant cost savings and sustainability benefits across diverse industrial applications. Companies are adopting innovative approaches to integrate these systems and maximize their efficiency.
Integration in Various Industries
Chemical manufacturers use pigging systems to recover valuable materials like paints, coatings, and adhesives. These systems push specially designed “pigs” through pipelines to clear residual product. Food and beverage producers implement similar techniques to reclaim juices, sauces, and dairy products.
Pharmaceutical companies employ advanced recovery methods for high-value medications and active ingredients. Oil and gas operators utilize pigging to clean pipelines and recover residual hydrocarbons.
Electronics manufacturers recover precious metals from production waste streams. This reclamation process reduces raw material costs and minimizes environmental impact.
Maximizing Efficiency and Reducing Costs
Optimizing product recovery systems involves strategic placement of equipment and fine-tuning of processes. Companies analyze production flows to identify key recovery points. Automated systems with sensors and controls enhance recovery rates.
Efficient cleaning operations reduce downtime between batches. This increases overall production capacity without major capital investments. Energy-efficient recovery methods lower utility costs.
Staff training programs ensure proper system operation and maintenance. This maximizes uptime and extends equipment life. Regular audits identify improvement opportunities and track cost savings.
Advanced Applications of Pigging Systems
Modern pigging systems handle complex pipeline configurations, including 90-degree elbows. This allows recovery in previously inaccessible areas. Bidirectional pigs enable efficient cleaning of branched networks.
Ultrasonic technology enhances pig detection and tracking. This improves system reliability and reduces manual monitoring needs. Smart pigs with onboard sensors gather pipeline condition data during recovery operations.
Multi-product pigging systems allow sequential recovery of different materials. This reduces cross-contamination risks in multi-use facilities. Specialized pigs made from advanced materials improve recovery rates for challenging products like high-viscosity lubricants and adhesives.
Conclusion
Product recovery systems offer significant cost-saving potential for industrial applications. By reclaiming usable materials from production lines, these systems reduce waste and minimize raw material expenses. They also lower cleaning and disposal costs while improving operational efficiency.
Implementing effective product recovery solutions can lead to substantial profit recovery for manufacturers across various sectors. As companies face tightening budgets, adopting these technologies becomes increasingly crucial for maintaining competitiveness and sustainability in today’s industrial landscape.