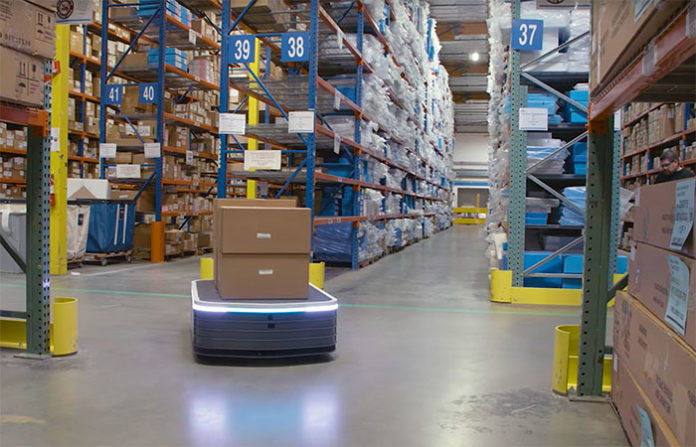
In modern warehouse operations, numerous processes need to be carried out smoothly to ensure efficient order fulfillment. With technological advancements, business managers increasingly rely on apps, digital management systems, and technology tools to enhance efficiency and reduce costs. One of the most exciting developments in this field is the integration of robotics.
Advancements in the warehousing industry have led to the development of specialized robots for various tasks. Warehouse robots manage inventory checks, assist with picking tasks, and more. Depending on the type of robot, they can:
- Sorting: Cobots can sort items based on size and dimensions, moving them from incoming shipments to specific bins or conveyors.
- Loading and Unloading: Robots with adaptive grippers can automatically load and unload items from shipment trucks.
- Transportation: AMRs and AGVs move inventory within the warehouse with minimal human intervention.
- Inventory Management: UAVs scan barcodes and QR codes to assess stock levels, using cameras to capture thermal information for monitoring temperature-sensitive goods.
- Picking: ASRS retrieve items from shelves and bring them to operators, reducing manual picking efforts.
- Packaging: Anthropomorphic robots pack items into boxes, adapting to different sizes and shapes for secure and efficient packing.
The most common types of warehouse robots include Autonomous Mobile Robots (AMRs), Automated Guided Vehicles (AGVs), Automated Guided Carts (AGCs), Automated Storage and Retrieval Systems (ASRS), Goods-to-Person (GTP) Robots, Palletizing and Depalletizing Robots, Sorting Robots, Automated Labeling Robots, Packaging Robots, Case Erectors, Cleaning Robots, Security Robots and Anthropomorphic Robots.
Advantages of Warehouse Robotics
Increasing Productivity
Robots excel at handling tedious, repetitive tasks, freeing up employees to focus on critical thinking projects. Packaging automation systems, for instance, manage the repetitive task of product packaging and fulfillment with high precision, increasing overall productivity without compromising quality. This can significantly enhance supply chain productivity by accelerating routine processes and minimizing common human errors.
Amazon’s use of Kiva robots (now Amazon Robotics) has significantly boosted the efficiency of their fulfillment centers. These robots navigate warehouse floors, bringing shelves to human pickers, thereby reducing the time employees spend walking and increasing the number of orders processed.
Reducing Mistakes
Automated systems reduce the likelihood of errors typically associated with human labor. Robots can navigate warehouses efficiently, reducing time spent moving between different areas and allowing employees to focus more on quality control.
In pharmaceutical warehouses, robots like Fetch Robotics’ Freight robots can transport medicines and medical supplies with precision, ensuring the correct items are delivered and reducing the risk of human error.
Improving Safety
Robots can operate in hazardous environments and work around the clock without posing a risk to human health. Equipped with sensors to avoid obstacles, they reduce the chances of serious accidents such as slips, trips, and falls from high ladders. This makes the workplace safer for employees, who no longer need to engage in risky manual tasks.
Ocado, a UK-based online grocery retailer, uses robots to handle heavy lifting and repetitive tasks in their warehouses. This reduces the risk of injuries related to manual lifting and repetitive strain, ensuring a safer work environment for their employees.
Easier Scheduling
Unlike human workers, robots do not need breaks and can work continuously over long shifts, leading to more efficient scheduling and higher overall productivity.
Robots in the DHL supply chain work continuously during peak seasons, such as the holiday rush, ensuring that the increased volume of orders is handled without the need for additional human labor shifts.
Quick Implementation
Robotic systems can be implemented relatively quickly—typically within four to six weeks, depending on the operation’s specifics. This is a remarkably short time compared to other technologies, such as Goods-to-Person (G2P) systems, which can take up to a year to implement.
6 River Systems’ Chuck robots can be deployed in a matter of weeks, allowing warehouses to quickly scale their operations to meet growing demand.
Ability to Scale
Robots offer modular deployment, allowing businesses to start with a few units and add more as demand grows. This flexibility helps avoid high initial investments and allows companies to gradually scale up their operations while assessing the impact of robots on their business.
Shopify’s distribution network uses modular robot deployment, enabling them to start with a small number of robots and expand their fleet as their order volumes increase.
Disadvantages of Warehouse Robotics
Job Elimination for Workers
While robots boost efficiency, they also pose a threat to warehouse employment growth. As robots take over more tasks, there is a risk of job elimination for human workers.
In some automotive warehouses, the introduction of robots has led to a reduction in the need for human workers to perform tasks such as parts sorting and assembly line feeding, resulting in job losses.
Lack of Adaptability and Ingenuity
Unlike humans, robots cannot adapt to changes in the workplace or use critical thinking to solve problems. They follow pre-programmed instructions and lack the ingenuity that human workers bring to dynamic environments.
During unexpected events such as system outages or non-standard order requests, robots may struggle to adapt, whereas human workers can quickly come up with creative solutions to address these issues.
Substantial Monetary Investment
The initial and ongoing costs of deploying robots can be high, especially for smaller warehouses. While robots can reduce labor costs by eliminating the need for employee benefits, companies must still cover maintenance and programming expenses. Skilled robotics programmers are also in high demand, adding to the overall cost.
A small e-commerce warehouse might find it challenging to justify the investment in a fleet of robots from a company like GreyOrange, given the high upfront costs and ongoing maintenance expenses compared to their current labor costs.