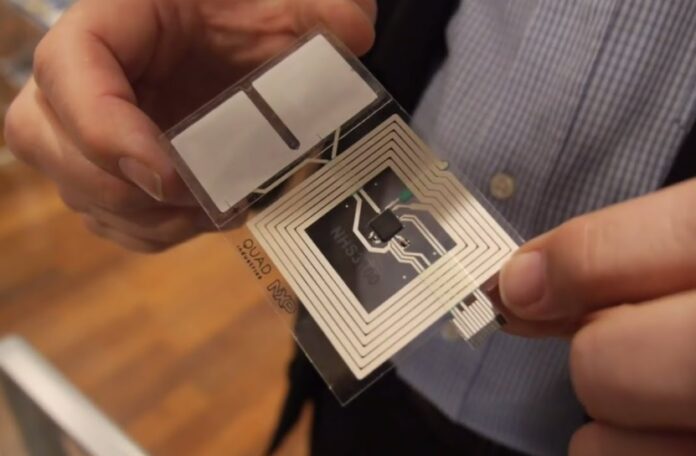
Printed batteries, also known as flexible batteries, are less than a millimeter thick, weigh less than a gram, and can be stretchable. They can deliver microwatts of power. Small devices, such as smart cards, sensors, RFID tags (for electronic identification), medical devices, and wearables, such as wristbands, are well suited. Their unique format opens up new possibilities for electronic labels, packaging, and posters for a new generation of electronics. It could help power the IoT (Internet of Things), a network of connected devices and everyday objects powered by small batteries.
Despite their novel format, printed batteries rely on existing chemical technologies such as lithium-ion. Depending on the materials used, they can be rechargeable or non-rechargeable. The electrodes and electrolyte are sandwiched between two sheets of a thin, flexible material (the ‘substrate,’ such as paper, plastic, or textiles). Ink is used to print these components onto the substrate. Alternatively, if the substrate is soaked in water and placed between the anode and cathode, it can be an electrolyte.
Printed batteries are already available for purchase. Non-rechargeable zinc-manganese dioxide printed on plastic substrates with over 1.6 volts is the most common commercially available printed battery. Wearables for monitoring (e.g., medical or sports performance) and electronic tags and cards are among these applications.
As production volumes increase, they become more cost-effective, and technology improves, printed batteries should become more commercially competitive. The inks are the most difficult aspect of their development. These should be better suited to print processes like ink-jet or screen printing, with the desired flow, adhesion, and structure. The inks must also have better ionic conductivity and mechanical and thermal properties to improve the battery’s performance.
While there are no environmental assessments for this technology, some indications and speculations exist. Individually, they use very little material; printing is a simple, ‘additive’ manufacturing process in which only the amount of material required is applied to the substrate. To remove excess material (which becomes waste) from components, more traditional and complex ‘subtractive’ processes use more energy and chemicals. Paper substrates are also a resource that is renewable, degradable, and recyclable.
However, the future proliferation of printed batteries poses an environmental risk; for example, billions of batteries will be required to power the internet of things, posing a significant environmental risk if not properly disposed of after use.
End-of-life (EoL) treatment poses several difficulties. Printed batteries are unlikely to be reused because they are designed for use in low-cost, often disposable, products with a short lifespan. Consumers are unlikely to consider e-waste. Recycling is also a problem because the materials are highly integrated, like conventional lithium-ion batteries. This challenge could be mitigated by using fewer materials.
They’re also likely to be embedded in products, making it difficult to separate them for reuse or recycling; once again, design for disassembly principles could help. According to researchers, it is possible to recycle paper products that contain printed batteries and remove the batteries in the recycling plant by sieving them out of pulped paper. On the other hand, the batteries were partially disintegrated after paper pulping in a small-scale experiment, and particles of their components were found to be likely to reduce the recycled paper’s quality. Due to the leaching of hazardous substances, landfilling printed batteries is also problematic.