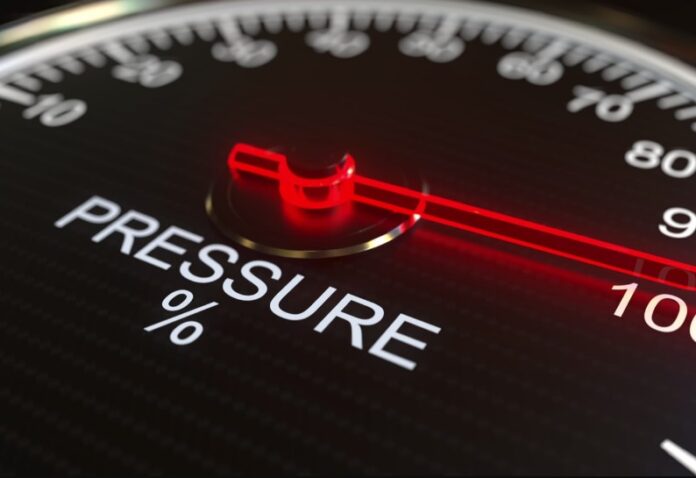
The pressure is one of the most important physical quantities in our environment. It is a significant parameter in industrial applications in disciplines such as thermodynamics, aerodynamics, acoustics, fluid mechanics, soil mechanics, and biophysics.
Most manufacturing units, automated or operated by human operators, require constant monitoring and control of pressures since overpressure could cause the deterioration of enclosures or drains and cause very significant damage to critical equipment types. Therefore, they use pressure sensors to monitor static or dynamic pressure changes and transform them into an analog electrical signal, where the applied pressure defines its quantity.
Pressure sensors are electro-mechanical devices that can identify forces in different types of gases and liquids: compressed air, gas, vapor, oil, atmospheric/barometric, pneumatic, water, liquid, hydraulic, and corrosive media and provide control signals to display devices.
Today, we use pressure sensors in various industrial applications ranging from HVAC/R compressors, refrigeration, air conditioning, touch screen devices, vehicle manufacturing, biomedical instruments, aviation, and variable speed pumps to hydraulic pressure, oil and water.
Pressure covers a very wide range from ultra-high vacuums to ultra-high pressures. It can be expressed as an absolute value (compared to vacuum) or a relative value (compared to atmospheric pressure). It can also represent a difference between two pressures or relate to various media and fluids with different physical (e.g., temperature) or chemical characteristics (e.g., risk of corrosion).
Today’s technologically advanced pressure sensors are more accurate, reliable, and rugged than ever before. They are best suited for long-term use even in harsh conditions with extreme temperature, humidity, and vibration. Pressure sensors are categorized into strain gauge type, capacitive pressure sensor, and piezo sensors. Piezo sensors, when combined with an IoT solution, can sense real-time changes in pressure.
This post will explore the advantages and disadvantages of three kinds of pressure sensors: capacitive, piezoelectric, and piezoresistive pressure sensors
1. Capacitive
Capacitive sensors display a capacitance change when pressure is applied to the diaphragm creating an oscillator frequency. Ideal for flow applications to measure gas or liquid pressures, they can be highly sensitive, measure pressures below 10mbar, and withstand large overloads.
Capacitive pressure sensors have several advantages over other types of pressure sensors. They can have very low power consumption because there is no DC current through the sensor element. The current only flows when a signal is passed through the circuit to measure the capacitance.
The sensors are mechanically simple, so they can be made rugged with stable output, making them suitable for harsh environments. Capacitive sensors are usually tolerant of temporary over-pressure conditions. However, constraints on materials and joining and sealing requirements can restrict applications.
Pros:
- Mechanically simple and robust.
- Suitable to operate in a wide temperature range from 2.5 mbar or 250 Pa to 10,000 psi (70 MPa)
- Very tolerant of short-term overpressure conditions
- Ideal for lower-pressure applications and reasonably harsh environments.
- Inherently low power because no DC current flows through the capacitor.
- Exhibit low hysteresis and a good repeatability of measurements.
- Have low-temperature sensitivity.
Cons:
- Non-linearity because the output is inversely proportional to the gap between the parallel electrodes.
- Sensitive to vibration.
- Material constraints can restrict applications.
2. Piezoelectric
Piezoelectric pressure sensors use the properties of piezoelectric materials such as quartz, rochelle salt, barium titanium, and tourmaline to create a charge which is proportional to the force applied on the surface when pressure is applied. The charge magnitude is proportional to the force applied, and the polarity expresses its direction. The charge accumulates and dissipates quickly as pressure changes, allowing measurement of fast-changing dynamic pressures.
Piezoelectric pressure sensors are widely used for dynamic pressure measurement in turbulence, blast, engine combustion, and some medical applications like monitoring arterial pulse. They can measure fast-changing dynamic pressures.
Pros:
- Very small and sensitive.
- Requires only a very small deformation to generate an output
- Measure a very wide range of pressures, between 0.1 psi and 10,000 psi (0.7 kPa to 70 MPa), with very high accuracy.
- Extremely robust and suitable for use in a range of very harsh environments
- Tolerate very high temperatures up to 1,000ºC.
- Self-powered and intrinsically low-power devices
- Insensitive to electromagnetic interference.
- Simple to construct from inexpensive materials.
Cons:
- Need high impedance circuit
- Unable to measure solid-state pressure due to dynamic nature
- A charge amplifier is necessary to convert the very high impedance charge output to a voltage signal.
- Only be used for dynamic pressure measurement.
- Susceptible to noise
- Sensitive to vibration or acceleration
3. Piezoresistive
Piezoresistive sensors are the earliest and most widely used type of pressure sensor. They take advantage of the change in resistivity of semiconductor materials when subjected to strain due to diaphragm deflection. The change in resistance is proportional to the strain caused by pressure on the diaphragm. Hence piezoresistive sensors can measure smaller pressure changes than metal or ceramic sensors. They are used for a wide range of pressure measurements from 3 psi to about 20,000 psi (21 kPa to 150 MPa). The output is stable over time.
Pros:
- Simple to construct
- Low cost and higher durability
- Good resistance to shock, vibration, and dynamic pressure changes.
- Circuits are very simple and enable high-resolution measurement
- Linear output and millisecond response time
- Operate at higher temperatures
Cons:
- The sensor has to be powered.
- Unsuitable for low power or battery-operated systems.
- Limitations on scaling down since it can reduce the sensitivity and increase the power consumption.
- Problems with the adhesives at high temperatures and overpressure.
- The output is temperature-dependent.