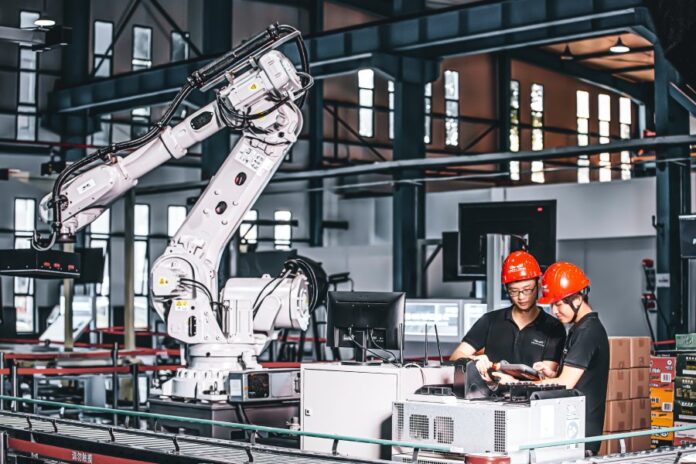
A robot is a machine that can automatically complete a complex series of tasks, especially one that a computer can program. It can mimic human behavior and stand in for people.
Robots can be employed for a variety of tasks and purposes. Many are still employed today in production processes, hazardous environments (such as the inspection of radioactive materials, bomb detection, and deactivation), and situations where humans cannot survive (e.g., in space, underwater, in high heat, and clean up and containment of hazardous materials and radiation).
An industrial robot is a robot system used for manufacturing. Industrial robots have three or more axes of motion, are automated, and can be programmed. Robots can be used for various tasks that require high endurance, speed, and precision, such as welding, painting, assembly, disassembly, picking and placing for printed circuit boards, packaging and labeling, palletizing, product inspection, and testing. They can help with handling materials.
Material handling robots
Material handling is a necessary but wasteful and expensive activity in manufacturing and distributing. Insufficient material handling accounts for additional costs in two main ways: idle time and cost of labor. Effective material handling solutions can significantly reduce a production or distribution facility’s cost.
Material handling robot refers to a system used in production and other industrial setups. It includes a battery-operated remote-sensing locomotive (carrier) on which a small lift is provided, a specific path over which it moves, and sensors for sensing the obstructions on the carrier’s path. Also, sensors for sensing exact positions from where the load wants to carry and to where.
One of the simplest ways to add automation is through material handling robots, which can automate some of the most tiresome, boring, and dangerous tasks in a production line. By delivering high-quality goods on time, material handling robots improve the productivity of your production line and raise customer satisfaction.
Many different product movements fall under the umbrella of material handling. A few material handling applications include part selection and transfer, palletizing, packing, and machine loading.
You should consider the payload and speed demands, the end-of-arm tooling or grippers required, the facility layout and floor space, the material being handled, and any additional potential production issues when choosing material handling equipment for your facility.
Benefits of Material handling robots
- Part transfer, a dull and tedious process, can also be injury-inducing to human workers. Adding robots to this job protects human workers from hazardous environments.
- Robots for packaging are very adaptable and simple to incorporate into a workspace. The benefits of packaging robots include faster part packaging, increased package lifting capacity, and lower labor costs. A robot can complete any packaging process with the appropriate end-of-arm tooling. Robot sizes, mounting choices, payload capacities, and reach come in a wide range.
- Palletizing robots can be seen in many industries, including food processing, manufacturing, and shipping.
- Machine-loading robots increase production speeds and protect workers from injury.
Material handling is an expensive, non-value-adding activity that can account for 30-75% of a product’s manufacturing cost. A typical manufacturing company dedicates 25% of its employees, 55% of its factory space, and 87% of its production time to material handling.
Deciding what material handling systems to utilize is important in creating an effective manufacturing or production system. Possible material handling systems include industrial trucks, conveyors, AGVS, cranes, AMRs, and stationary robots.