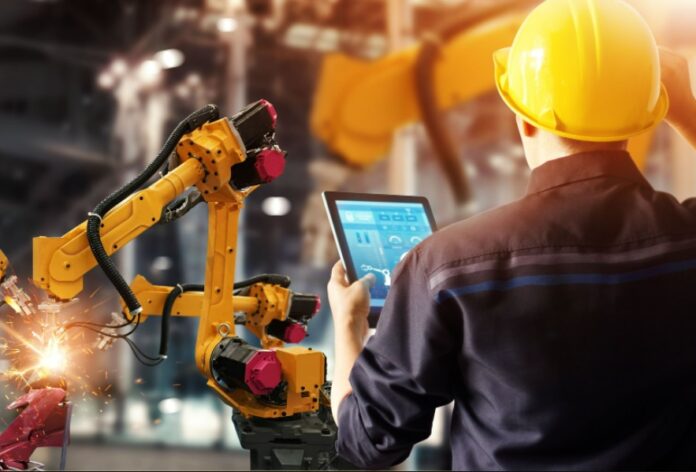
Accessible robotics training will ensure employees build the manufacturing skills they need as technology revolutionizes the industry. Manufacturing companies are grappling with a growing skills gap. Technology is becoming more and more important to success, but manufacturing employees struggle to keep up.
There is a solution to both of these problems. By creating easily accessible robotics training programs, manufacturing companies can train their employees to fill the skills gap and empower them to upskill into more advanced careers.
Robotics Training and the Skills Gap
A digital transformation is sweeping the manufacturing industry. Robotics is at the heart of this transformation. Other technologies, like AI and the Internet of Things (IoT), are also having a major impact on manufacturing, but none to the extent of robotics.
Industry 4.0 is making manufacturing smarter, more cost-efficient, more sustainable, and better optimized. Unfortunately, with new technology comes a need for new skills in the workforce. Manufacturing technology is advancing so rapidly that employees struggle to find the time and money to get training to update their skills. Awareness of trade and technical careers, such as those in manufacturing, is decreasing in junior high and high schools.
Some of the 2021 studies predict that there will be over 2 million unfilled jobs in manufacturing by 2030. One of the biggest issues is the ongoing difficulty of finding the right talent. Current employees lack the necessary skills for emerging technologies, and new employees with those skills are difficult. Robotics expertise is key among these skills.
The manufacturing skills gap can be attributed to several factors. Industry experts have pointed out that the aging workforce in manufacturing results in a wave of retiring workers.
Regardless of whether these employees possess cutting-edge skills, their experience in their specialties is extremely difficult to replace. The COVID-19 pandemic is leading many people to retire early, as well. Younger generations’ stigma toward trade careers only furthers long-term and short-term hiring troubles.
Robotics training could be a crucial solution to the skills gap. Creating easy-access robotics training benefits both employers and employees. Existing employees can be empowered to build manufacturing skills in new niches of the industry, while outreach training programs help attract new talent. Both results will bridge the skills gap and help manufacturers reap the benefits of Industry 4.0 technology.
Training Internally and Externally
Robotics training can be used to build manufacturing skills within manufacturing companies and in schools and educational programs. These training programs benefit both the manufacturing and robotics industries.
Internal training programs at manufacturing companies help current employees adapt to new technologies. These robotics training programs are also a great way for robotics professionals to network with manufacturing companies through new applications for robotics in manufacturing.
For long-term growth, industry leaders should consider creating external training programs for local high schools, technical schools, and community colleges.
An easy-access robotics training program should prioritize affordability and flexibility. If possible, it should be completely free for students, especially if it is an internal program. This generally means the program’s cost will fall on manufacturing companies. So, robotics professionals may earn some extra income by offering their knowledge and expertise for training programs.
This is an investment for manufacturing companies, not an expense. They are investing in the skills of current employees and investing in the training of future employees.
The Importance of Outreach
External training programs will be particularly important in the years ahead. The manufacturing industry desperately needs new young professionals, and a unique window of opportunity is appearing with today’s generation of junior-high and high-school students. There has rarely been a better time for both the robotics and manufacturing industries to develop outreach robotics training programs.
The COVID-19 pandemic has left many Gen-Z high school students questioning the value of a four-year degree program. Gen-Z students pursuing college degrees dropped from 71% down to 48% between May and September 2021. Meanwhile, interest in trade and tech schools is on the rise.
“Zoomers” are more open to other options than high schoolers in previous years have been. This is a great opportunity to introduce young people in local communities to careers in robotics and manufacturing. Gen-Z students look for valuable education, hands-on experience, and a rewarding career – not necessarily a prestigious degree or a traditional college experience.
Zoomers are also digital natives, meaning cutting-edge technologies will come naturally to them. So, offering free introductory robotics training to local high-school students could lead to a wave of skilled new employees comfortable with tech and digitalization. Many students may not even be aware that robotics, engineering, manufacturing, or technical trades are a good fit for them, so outreach is so important.
Upskilling and Building Manufacturing Skills Internally
Internal robotics training can provide an immediate return on investment for manufacturing companies, making it a high-value niche for robotics training professionals. Rather than spending money to hire new employees, that money can be directed to training for existing employees. Manufacturing companies can equip their employees with the exact skills needed for their robotics initiatives. This is much more straightforward than searching for job applicants who already have the necessary skills.
Upskilling is great for employees, as well. Technology is only going to become more prevalent in manufacturing with Industry 4.0. So, employees need to build manufacturing skillsets that include robotics. Encouraging employees to continue learning new manufacturing skills will future-proof the workforce and enable manufacturing companies to innovate and grow.
It is also important to note that the relationship between robotics and manufacturing jobs can be highly beneficial. Some employees may worry that robots will “take” their jobs one day. This is a valid concern, but robotics training can result in the opposite effect.
Robotics is expected to create jobs in manufacturing over the years ahead. While robots may be replacing humans in mundane and repetitive tasks, new jobs will be created for robot maintenance, installation, and operation. Skilled manufacturing employees will even be needed to help build more new robots.
Creating a Robotics Training Program
Robotics training programs will differ depending on the specific goals a manufacturing company or educational institution has in mind. Some types of robots may require more training than others. However, some general best practices will help a new robotics training program get off to a good start.
Internal Training
Robotics professionals looking to organize a training program for manufacturing employees must keep a few things in mind. Scheduling and promotion will likely be the biggest challenges manufacturing companies face when trying to host a training program.
Robotics professionals will need to work with company leaders to ensure the program is easy for employees to attend in between their everyday work responsibilities to ensure good attendance.
Additionally, it is important to explain the benefits and goals of robotics training to employees. As mentioned above, some may be wary that robots and automation endanger their jobs. Clarifying the benefits of upskilling and learning how to use robots will help resolve these concerns. It will motivate employees to build manufacturing skills through the training program and increase engagement.
Keep internal training programs approachable, but remember that employees will already have a foundational knowledge of manufacturing. Don’t be afraid to let employees dive right in. Be sure to make a clear connection between the technology they learn about and its applications on the manufacturing floor.
Community and Outreach Training
Community-based and outreach robotics training requires a slightly different approach than internal training. For instance, first, robotics professionals and companies will most likely have to reach out to local schools. It may be helpful to already have an outline for the training program or presentation. Still, robotics professionals can work with local educators to create customized experiences for students.
This type of training needs to be engaging from start to finish, especially for junior-high or high-school programs. The idea is to educate students while also getting them excited about careers in robotics and manufacturing. If possible, a younger employee may make a good presenter since they may be more relatable to students.
Robotics training is the perfect way to build manufacturing skills in schools. Today’s students are already excited about robotics, so demonstrating how they can apply that interest to manufacturing will go a long way.
Make sure to offer a way for students to get in contact or learn more about any robotics or manufacturing topics discussed. Single presentations should generally come at little to no cost for the school. Formal training programs or camps may have tuition, but keeping the program affordable for families and students is crucial. Robotics professionals can even work with local manufacturing companies to organize a sponsorship for the program.
Build Manufacturing Skills for the Future
Industry leaders, current employees, and future robotics and manufacturing professionals need to build manufacturing skills if they want to prepare for the tech-powered future. Accessible robotics training is the ideal way to do this and benefits everyone involved.
Manufacturing companies need to bridge the skills gap. Current employees want to future-proof their skills. Young people want rewarding jobs in technical fields. Robotics training will build the manufacturing skills that drive innovation, growth, and the future of the manufacturing industry.